Industrial Plating Company uses chromium carbide coatings to give our customers a way to protect their components and machinery from abrasive wear in high temperature and corrosive environments. Applied typically through HVOF spray technology, chromium carbide is comprised typically of powdered tungsten, cobalt, and chromium.
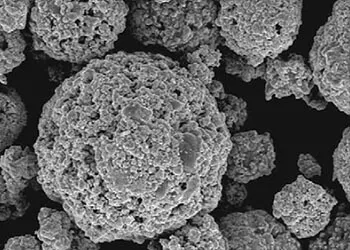
Chromium Carbide SEM Image
Tungsten Carbide 10% Cobalt 4% Chromium
Corrugating rollers, pump seals, hydraulic rods, pump piston rods, compressor shafts, paper and textile rolls, hard chrome alternative.
Provides good wear and corrosion resistance.
Chromium Carbide 37% Tungsten Carbide
Pumps housing and impellers, boiler tubes, and chemical processing plant equipment components
Good wear resistance with better corrosion resistance in alkaline, sulfuric, or saline solutions
Chromium Carbide 25% Nickel Chromium
Hydraulic cylinders and piston rods, valve stems, turbine components, pump housings
Good wear resistance and excellent corrosion resistance in NaOH, NaCl and acidic environments. Avoid HCl solutions.
Tungsten Carbide 9% Cobalt 5% Chromium 1% Nickel
Mining rollers, pump seals, paper and textile rolls, hydraulic cylinders, hard chrome alternative.
Good wear resistance with excellent corrosion protection in NaCl, good in HCl, sulfuric, and sodium hydroxide.
Chromium carbide coating applications that require smooth surface finishes must be ground with diamond abrasives. Industrial Plating has
cylindrical grinding and
surface finishing capabilities and expertise to meet your requirements.
These are just a small sample of the coatings that we offer. Additional materials with different performance properties are available to meet the specific needs of your application.
We have over 50 years of experience applying plating and coating on a vast range of industrial machinery and equipment.
Contact Industrial Plating Company today, and learn about chromium carbide uses and the options we have available.